Printing
Welcome to a new era of printing – LED flexo printing!
Immerse yourself in a world of brilliance, efficiency and environmental awareness. With our LED flexo printing technology, we have once again done pioneering work. Together with our ink supplier, we have reached a completely new level and set standards in terms of quality and sustainability.
Advantages:
- LEDs consume significantly less energy compared to UV lamps, resulting in considerable energy savings and resource conservation.
- Shorter curing time of the inks, which helps to achieve higher production speeds and thus increases the efficiency of the printing process.
- LED inks are free of harmful solvents and VOCs, minimising emissions. LEDs do not produce ozone.
- LEDs have a much longer lifespan and therefore generate less waste.
- LED inks produce even sharper details and more vivid colour images.
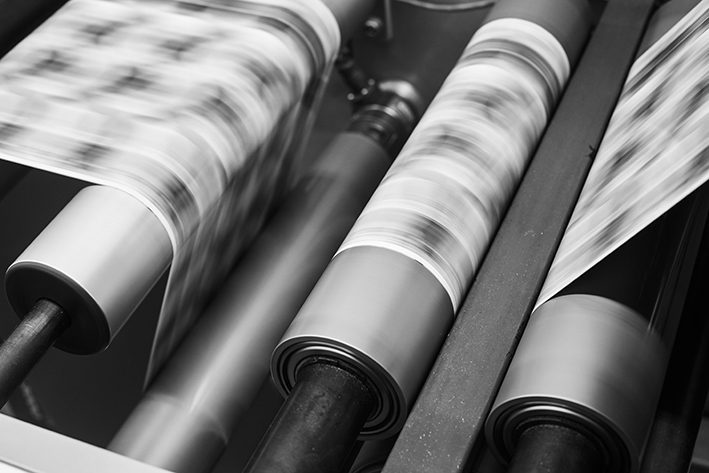
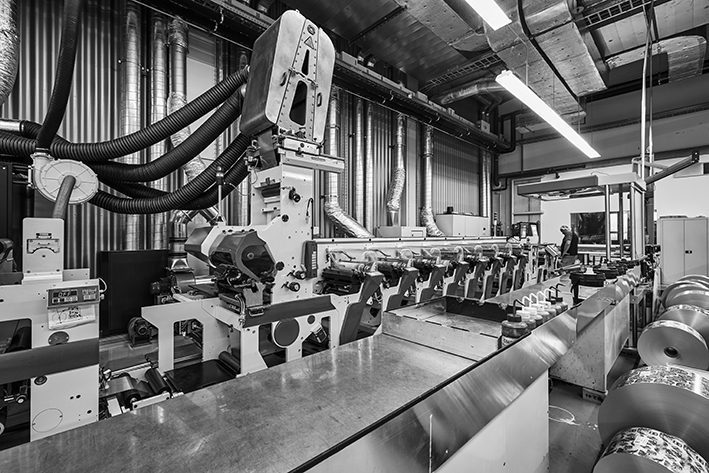
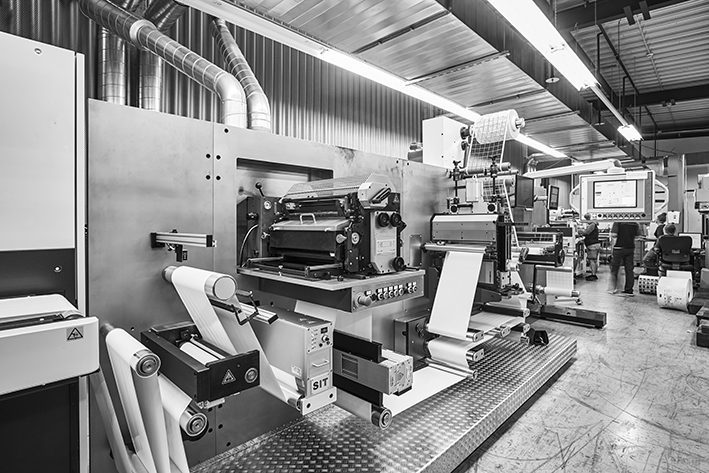
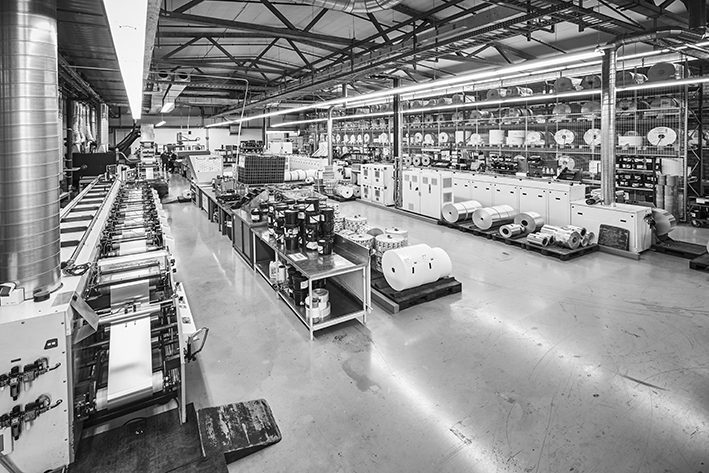
Digital printing
Our goal – cost-optimized production
Next-generation lid and label production. Inkjet, unlike conventional printing processes such as UV flexo, offset or gravure, is a non-contact printing process and therefore does not require printing plates.
Countless advantages
- No printing plates, less ancillary costs!
- Low-migration printing inks
- Wide color range
- High opacity of colors
- No register differences
- 100% reproducibility of print jobs
- Hardly any waste during production
- Sustainability and conservation of resources
- Affordable small series for test markets etc.,
- Personalizable design, variable printing of serial numbers
- (there are completely new marketing options, e.g. regionalization, profit codes,etc.)
- Very flexible delivery times
- Proofs on original material and 100% match to the print run